Tratamiento y pintado de Aluminio
Preparacion del aluminio para pintarlo.
Cuando el aluminio se expone al aire, se forma una superficie de oxido que protege el metal en muchos ambientes. Desafortunadamente, el oxido natural no es uniforme y puede ocurrir una corrosión localizada Tampoco el oxido es estable con pH bajo o alto. La solubilidad con pH elevado crea problemas debajo de la pintura.
Pre-tratamiento
Una de las formas de mejorar la resistencia a la corrosión del aluminio pintado, es tratar la superficie químicamente para hacerla más pasiva. El pre-tratamiento o capas de conversión producen una reacción en la superficie, convirtiendo el oxido en una película relativamente inerte que proporciona una buena adhesión para la pintura y mejora la resistencia contra la corrosión. Esta película puede ser amorfa o cristalina, dependiendo del pre-tratamiento utilizado.
Efecto de la aleación
La razón final de cualquier producto de pre-tratamiento, es de consideración determinante en la selección de un sistema de pre-tratamiento y pintura. El ambiente de utilización (en el exterior o en el interior) y la expectativa de duración para su uso, son factores clave. En el aluminio, su uso final afecta, también, la selección de la aleación correcta. Elementos de aleación se añaden al aluminio para potenciar sus propiedades mecánicas y físicas.
Tabla l. Aleaciones de Aluminio Comunes
Aleación | Elemento | Utilización de las principales aleaciones |
---|---|---|
2000 | Cu | Alta resistencia - Aviones |
3000 | Mn | Latas |
5000 | Mg | Estructuras - Arquitectura |
6000 | Mg, Si | Extrusionado |
7000 | Zn, Mg, Cu | Alta resistencia - Aviones |
La tabla l relaciona las aleaciones que se encuentran en operaciones de pre-tratamiento, los elementos de las principales aleaciones y aplicaciones típicas para las aleaciones. La presencia de elementos de aleación puede afectar la resistencia a la corrosión. Por ejemplo, aunque se usa el cobre para aumentar la resistencia, ello disminuye la resistencia de corrosión del aluminio, mas que ningún otro elemento de aleación. Asimismo, ciertos elementos de aleación forman una mancha negra al limpiarlo con alcalinos. El metal manchado puede requerir una fase separada de desoxidacion con ácido, antes del pre-tratamiento. Por ello, debe conocerse el tipo de aleación y el fin para el que va a ser utilizado.
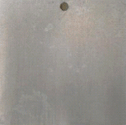
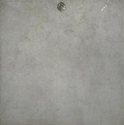
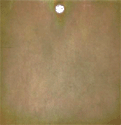
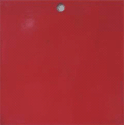
Visión de conjunto del proceso
En la figura 1 se muestra un ejemplo de la secuencia de un proceso de pre-tratamiento. En este proceso, dos secuencias principales –limpieza y pre-tratamiento- requieren el uso de productos químicos. Se requiere un aclarado intermedio para quitar los residuos químicos y las sales inadhesivas.
Limpieza
Los contaminantes en la superficie del aluminio varían según la aleación y el proceso de fabricación utilizados para manufacturar la pieza. Las piezas hechas a maquina, taladradas, Cortadas, agujereadas o formadas, tienen aceite o taladrinas en la superficie. Ates de poder aplicar un pre-tratamiento, estos contaminantes deben ser quitados para que el pre-tratamiento de base acuosa pueda mojar completamente la superficie. Si no esta mojado por completo, el resultado será una película sin uniformidad de baja calidad.
La limpieza de una superficie puede ser definida por producir una película de agua que no se rompa tras el aclarado. La rotura de la película de agua indica la presencia de suciedad orgánica. Como prueba, si se pasa un paño blanco, este mostrara la presencia de suciedad orgánica. Esto ocurre en especial, con aleaciones que contengan cobre, magnesio o silicona, que pueden producir manchas durante la limpieza. Las manchas (óxidos de alcalinos insolubles de elementos de aleación) si no son eliminados, producen una película de pre-tratamiento desigual o sin adherencia. Varios factores tienen influencia al escoger el tipo de limpieza, incluidos las aleaciones, los contaminantes presentes y el numero de fases y tiempo de contacto disponibles para la limpieza.
Productos de desengrase que dejan marcas (“Etching”)
Los desengrases alcalinos pueden ser clasificados como los que dejan marcas (Etching) o sin dejar marcas (non-etching). Un desengrase que deja marcas (etching) aprovecha las ventajas de la solubilidad del aluminio con un elevado pH. Además de quitar suciedad orgánica, un desengrase de este tipo, disuelve la película de oxido de la superficie y quita algo de la base metálica. Las imperfecciones de la superficie, tales como arañazos o manchas de agua pueden efectivamente quitarse con este método.
El tiempo de desengrase es otro factor importante en la formulación del producto de limpieza.
Donde el tiempo de contacto es breve, un producto de limpieza muy formulado con varios tensoactivos puede necesitarse. Ello asegura que el desengrase rompe cualquier aceite muy rápidamente, con lo que puede obtenerse un dibujo (etching) uniforme. Un problema potencial que crean los desengrases es la formación de aluminio en el baño de desengrase y la precipitación de hidróxido de aluminio. Si ello no se controla, precipita y puede acumularse en las paredes de la cuba y al calentar la superficie, obtura las boquillas de los sistemas de aspersión (spray).
Desengrasantes sin marcas (“Non-Etching”)
En algunas aplicaciones, tales como la limpieza de una superficie de aluminio pulimentada, es preferible la limpieza si apagar el brillo del pulido. Los desengrasantes sin marcas (Non-Etching), producen una superficie limpia, sin disolver el metal de la superficie. El pH de la solución desengrasante parece jugar un papel importante en la habilidad para inhibir el ataque. La selección de tensoactivos es básica para tener éxito, porque la acción de limpieza no implica ataques agresivos de la superficie interna del aluminio.
Desoxidantes
Debido a que la limpieza con soluciones de base alcalina puede producir manchas y/o una superficie de oxido desigual, se han utilizado desde hace tiempo desoxidantes/quita manchas en algunas operaciones de pre-tratamiento, para completar la limpieza de la superficie.
Las mezclas de ácidos fuertes no desoxidan uniformemente la superficie, propiciando partes que son mas susceptibles a la corrosión por hoyos (“pitting”). Los desoxidantes con una base de cromo han sido utilizados con éxito desde 1940 para desoxidar apropiadamente las superficies de aluminio.
Pre-tratamientos
Los pre-tratamientos para el aluminio son ácidos y aprovechan la baja solubilidad del aluminio y su oxido. Como se ha indicado anteriormente, ello se produce al convertir la capa de oxido de la superficie en una forma más pasiva.
Los sistemas de pre-tratamiento que se usan pueden ser de las siguientes categorías.
* Tratamientos convencionales de cromatizados y fosfato de cromo.
* Tratamiento de cromo sin aclarado.
* Tratamientos no Cromicos.
* Tratamiento de zinc o fosfato de hierro para aplicación en metales múltiples.
Tratamientos convencionales con base de cromo
Los dos procesos convencionales para aluminio-fosfato de cromo y cromatizados- utilizan una solución de ácido cromico para atacar la superficie de oxido y oxidar la base del metal. El ácido se consume al reaccionar, dando como resultado un aumento localizado del pH en la superficie y las interfases de las capas. Tal aumento del pH conduce a la precipitación de una película con base de cromo. La composición del recubrimiento y su comportamiento difieren significativamente en los dos procesos.
Fosfato de cromo
El proceso de fosfato de cromo de hoy en día, procede de mediados de los años 40. Es la opción predominante en el pre-tratamiento del aluminio extrusionado. Cuando la solución entra en contacto con la superficie, actúa inicialmente como un desoxidante, continuando con la esencialmente el proceso de limpieza. La acción desoxidante puede quitar imperfecciones de la superficie, que hayan sido causadas durante el proceso de extrusion y manchas formadas duran te la limpieza.
Los análisis efectuados en recubrimiento de fosfato de cromo indican que el recubrimiento es una mezcla de fosfato de cromo, oxido de cromo y fluoruro de aluminio y óxidos. Las muestras de cromo son dominantes en las capas más externas del recubrimiento, encontrándose aluminio trivalente en la interfase del metal/pre-tratamiento. Para aplicación en extrusionados, el peso del recubrimiento normalmente es de 160 a 240 mg/cm2 para un comportamiento optimo. Cuando el recubrimiento es mas pesado, este tiende a ser polvoriento y la adhesión de la pintura puede resentirse.
Cromatizado
Los recubrimientos de cromatizado pasan las especificaciones militares ASTM sobre resistencia a la corrosión sin pintura y son los pre-tratamiento dominantes para aplicaciones aeroespaciales.
La solución de tratamiento, aspecto del recubrimiento y composición del recubrimiento, difiere significativamente por el proceso de cromatizado. Los recubrimientos son de un color irisado/dorado en comparación con los recubrimientos de fosfato de cromo irisados/verde.
Generalmente se ha creído que la superior resistencia a la corrosión de la película de cromatizado, era debida a la presencia de cromo hexavalente en la capa de pre-tratamiento. Sin embargo, continua existiendo un debate sobre si el cromo hexavalente esta presente en la capa una vez seca.
Tratamientos no crómicos.
Los tratamientos de superficie libres de cromo de hoy en día para el Aluminio y sus aleaciones, se vienen desarrollando y probando con logrado éxito en los últimos años.
La resistencia a la corrosión del metal tratado y la adherencia de los recubrimientos, han tenido una mejora sustancial.
Aunque la Performance de los procesos crómicos no ha sido superada, estos productos a base de Titanio o Zirconio están teniendo muy buenos resultados, y constituyen hoy, la alternativa ecológica en reemplazo de los tratamientos convencionales.
Tecnología a base de sales de Zirconio o Titanio
Producto | Base | Aplicación |
---|---|---|
N.C. | Zr | Partes en General |
N.C. | Zr | Perfiles* |
N.C. | Ti | Perfiles |
N.C. | Zr | Llantas |
-Solución acuosa
-Concentración de 2 al 5%
-Temperaturas de 40 a 80 C
-Tiempos de tratamiento de 0.5 a 5 min.
*Aplicación DIP (sin enjuague final)
Proceso de anodizado
Actualmente también se aplica por cuestión medio ambiental y la corrosión filiforme, el anodizado con base de ácido sulfúrico convencional, con desengrase –satinado si lo precisara- desoxidante con sulfuro mas aditivo, por el problema que representan los nitratos y nitritos en el medio ambiente y un anodizado de 5 u en que la capa porosa y no porosa hacen un gran anclaje y no se ve afectada la capa barrera, pues de esta manera se abre mucho mas el poro.
Aplicaciones multimetales
Muchas operaciones de acabado se enfrentan con el reto de tratar el aluminio, el acero y el acero galvanizado. Característicamente, las operaciones de tratamiento por separado no son una opción viable. El enfoque correcto esta dictado por el uso final del producto acabado. Para aplicaciones en metal fabricado, el tratamiento a escoger viene dado principalmente por el hecho de que la aplicación sea interior o exterior. Para aplicaciones de gran calidad exterior de piezas de automoción, puede aplicarse un recubrimiento de fosfato de zinc en los tres substratos, si hay suficiente fluorhidrico presente en el baño de tratamiento para aislar el aluminio disuelto. Para aplicaciones menos importantes o criticas, en las que la adhesión de la pintura no es una preocupación esencial, un proceso de fosfato de hierro puede utilizarse.
Conclusiones
Se dispone de varios procesos para mejorar la adhesión de la pintura y la resistencia a la corrosión del aluminio. La selección del sistema de pre-tratamiento del aluminio comienza con un análisis de la utilización final de producto acabado. La composición química del aluminio y el tipo de aleación, así como consideraciones del entorno ambiental, tienen también un impacto en la selección del proceso de pre-tratamiento.